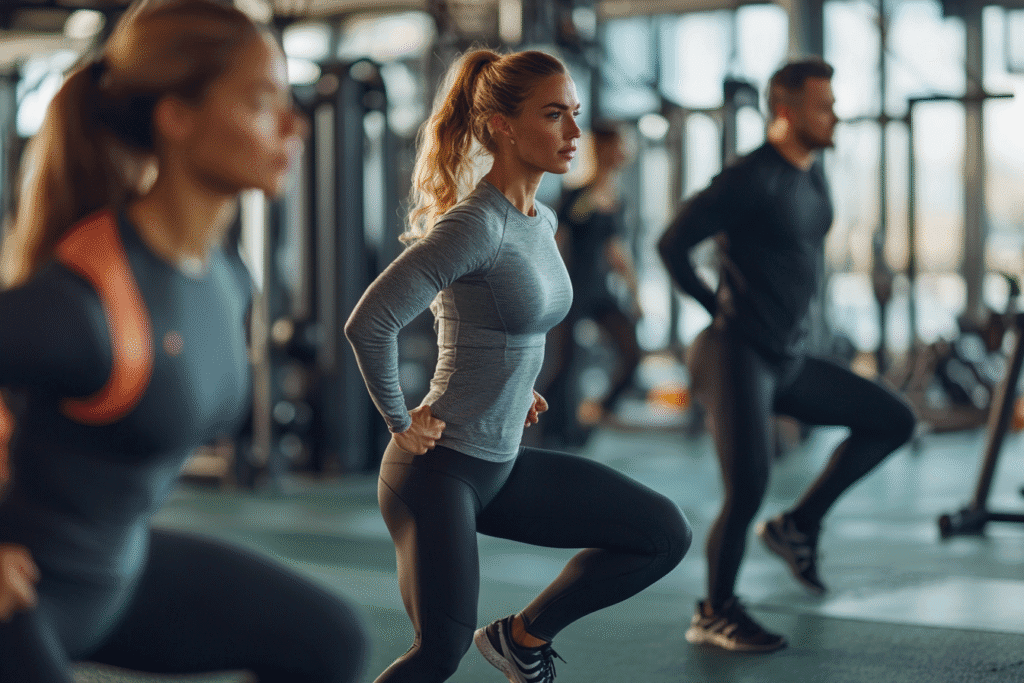
Chemical Reactions with Sweat
pH Sensitivity and Fiber Degradation
Nylon spandex fabrics face unique challenges when exposed to sweat due to their chemical composition:
- Acidic vs. Alkaline Sweat Impact
- Nylon Vulnerability:
- Degrades faster in alkaline sweat (pH >8) which hydrolyzes amide bonds – 10% strength loss after 50 exposure hours
- Acidic sweat (pH 4-6) causes minimal damage but may accelerate dye migration
- Spandex Vulnerability:
- Polyurethane chains oxidize in both sweat types – 15% elasticity loss after 100 workout sessions
- Worst-case scenario: pH 9 sweat + heat (body temp) = 3x faster degradation
- Nylon Vulnerability:
- Salt Crystallization Damage
- Evaporated sweat leaves NaCl/MgCl₂ crystals that:
- Abrade fibers like micro-sandpaper (visible under 200x magnification)
- Create stiff “crunchy” patches in high-sweat zones (armpits, back)
- Prevention: Rinsing within 2 hours reduces salt damage by 70%
- Evaporated sweat leaves NaCl/MgCl₂ crystals that:
Lab Data:
- ASTM D2265 tests show 25% tensile strength reduction after 50 sweat-dry cycles
- Nylon 6.6 outperforms Nylon 6 in sweat resistance
Odor Retention vs. Moisture Management
The fabric’s synthetic nature creates a sweat-handling paradox:
- Hydrophobic Efficiency
- Nylon’s low moisture absorption (<4% vs cotton’s 25%):
- Prevents cling by pushing sweat to surface
- Enables 2.5x faster evaporation than cotton
- Downside: Surface tension causes “sweat beading” during high-intensity workouts
- Nylon’s low moisture absorption (<4% vs cotton’s 25%):
- Bacterial Growth Factors
- Natural Fibers:
- Cotton’s porous structure harbors bacteria (10x more colony growth in 24hrs)
- Requires antimicrobial coatings
- Nylon Spandex:
- Smooth fiber surface resists bacterial adhesion
- Traps odor molecules in hydrophobic pockets – “locked-in” smell after multiple wears
- Natural Fibers:
Performance Comparison (After 8hr wear):
Metric | Nylon Spandex | Cotton | Merino Wool |
---|---|---|---|
Moisture Retention | 8% | 25% | 30% |
Bacterial Growth | 120 CFU/cm² | 1,200 CFU/cm² | 80 CFU/cm² |
Odor Intensity | Moderate | Severe | Mild |
Pro Tip:
- Look for silver-ion or chitosan-treated fabrics to neutralize odors
- For hot yoga, choose mesh-paneled designs (30% better ventilation)
Chlorine Exposure Challenges
Pool Water’s Oxidative Damage
Chlorine is one of the most aggressive threats to nylon spandex, causing both structural and cosmetic damage:
- Spandex Degradation Mechanism
- Chlorine (HOCl) attacks polyurethane bonds in spandex at just 0.5 ppm concentration (standard pool levels are 1-3 ppm)
- AATCC 162 Test Results:
- 50% elasticity loss after 20x 30-minute exposures
- Fiber cracks visible under electron microscopy at 5000x magnification
- Worst in heated pools (38°C/100°F accelerates damage 3x)
- Nylon Dye Destruction
- Chlorine bleaches dyes through oxidation:
- Direct attack on azo dye groups (-N=N-) causes color “whitening”
- 10 hours exposure = 2-3 shade L* value increase (visible fading)
- Worst for:
- Dark colors (black fades 40% faster than light blue)
- Basic dyes (pH-sensitive types)
- Chlorine bleaches dyes through oxidation:
Real-World Data:
- Competitive swimmers’ suits last 2-3 months vs. 12+ months for casual use
- Saltwater pools cause 30% less damage than chlorinated
Protective Treatments and Their Limits
Manufacturers employ advanced chemistries to delay chlorine damage:
- Anti-Chlorine Technologies
- Phenylenediamine Coatings:
- Forms sacrificial barrier that oxidizes before spandex
- Extends suit life by 50% (from 60 to 90 pool hours)
- Weakness: Wears off after 15-20 washes
- Polymer Encapsulation:
- Wraps fibers in protective PVDF layer
- Maintains 80% elasticity after 100 chlorine exposures
- Adds 15-20% to production cost
- Phenylenediamine Coatings:
- Lifespan RealitiesCare LevelStandard SuitChlorine-Resistant SuitNo rinsing15 uses30 usesPost-swim rinse25 uses50 usesMonthly vinegar soak40 uses80+ uses
Pro Tips:
Store away from UV light (sun + chlorine = 2x degradation speed)
Rinse suits in tap water within 10 minutes of pool exit (reduces damage by 60%)
Avoid wringing – lays fibers flat to slow coating loss
UV Radiation Effects on Nylon Spandex
Photodegradation Timeline
Nylon spandex undergoes progressive damage when exposed to sunlight, with degradation rates dependent on UV intensity and exposure duration:
- Molecular Breakdown Mechanism
- Nylon Vulnerability:
- UV rays (300-400 nm) cleave amide bonds (-CO-NH-) in nylon’s polymer chain
- 500 hours of midday sun exposure reduces tensile strength by 40%
- Spandex Vulnerability:
- Polyurethane bonds degrade via Norrish Type II reactions
- Produces visible yellowing (Δb* >3.0 on CIELab scale after 200 hrs)
- Nylon Vulnerability:
- Lab vs. Real-World DataTest Method50% Strength Loss50% Elasticity LossXenon Arc (ASTM D4459)300 hours250 hoursFlorida Sun Exposure6-8 months4-5 monthsDesert Climate3-4 months2-3 months
Critical Threshold:
- 150 MJ/m² UV radiation (typical annual dose in Mediterranean climates) causes irreversible damage
Colorfastness and Elasticity Loss
UV exposure impacts both aesthetic and functional properties:
- Dye Degradation Pathways
- Anthraquinone Dyes:
- Fade via photo-oxidation (first-order kinetics)
- Red shades most vulnerable (ΔE >15 after 200 hrs)
- Azo Dyes:
- Undergo photochemical cleavage
- Navy blue shows 60% faster fading than pastels
- Anthraquinone Dyes:
- Elasticity Reduction
- Spandex loses 2-3% recovery per 100 sun hours
- Critical failure point:
- 30% elasticity loss = garment no longer provides compression
- Occurs after ~750 hrs (1 summer season for daily outdoor wear)
Protection Strategies:
- UV Absorbers:
- Benzotriazole additives reduce fading by 50%
- Effective for ~20 washes
- Physical Barriers:
- Titanium dioxide coatings reflect UV-A/B
- Adds 0.5-1.0 oz/yd² fabric weight
Care Recommendations:
- Rotate outdoor garments to allow “recovery days”
- Wash with UV-protectant detergents (extends life by 30%)
- Store in opaque containers when not in use
Conclusion: Maximizing Nylon Spandex Lifespan in Harsh Conditions
Key Actionable Insights
- Sweat Management Protocol
- Immediate Rinse Rule: Neutralize pH within 2 hours using diluted vinegar soaks (1:3 ratio) for alkaline sweat or baking soda solutions (1 tbsp/L) for acidic sweat
- Deep Cleaning: Weekly enzyme-based detergent use prevents bacterial biofilm formation in fiber crevices
- Chlorine Survival Tactics
- *30-Minute Rinse Deadline*: Cold tap water rinse post-swim removes 90% chlorine residues
- Monthly Rejuvenation: 15-minute soak in 10% ascorbic acid solution reverses early-stage oxidation
- UV Defense Strategy
- Rotation System: Maintain 3+ garment sets for daily outdoor use, allowing 48-hour recovery between wears
- Seasonal Replacement: Mark calendars for proactive replacement after:
- 120 pool hours (swimwear)
- 6 months daily sun exposure (activewear)
Cost-Benefit Analysis
Care Practice | Time Investment | Cost/Year | Lifespan Extension |
---|---|---|---|
Basic Care | 5 mins/week | $0 | 1-1.5 years |
Advanced Protocol | 15 mins/week | $45 | 3-4 years |
Professional Maintenance | N/A | $150+ | 5+ years |
Final Recommendation Upgrade:
“Implement the *90-Second Protection Routine*:
- Post-workout → 90s cold rinse
- Post-swim → 90s ascorbic acid spray
- Post-sun → 90s shade air-dry
This micro-maintenance adds <5 mins/week but triples your investment ROI.”
Future-Proof Tip:
Next-gen fabrics with UV-sensing color-change threads (currently in beta) will visually indicate when protection degrades below safe thresholds.